Causes & solutions
Defect patterns in powder coatings
Various defects can occur in powder coatings, which are not only aesthetically unpleasant, but also have a negative impact on the quality and use of the coated object. They have various underlying causes and can occur throughout the entire coating process. They range from problems caused by inadequate pre-treatment of the substrates to the application of uneven powder coating thicknesses and damage during the curing process.
The various challenges of powder coating
Even inadequate preparation of the surface of the object to be painted can result in the paint coating applied not adhering, adhering insufficiently or adhering unevenly. This can also quickly lead to the inclusion of impurities, which are particularly visually unattractive but can also lead to a reduced protective function of the coating.
The application of the powder coating also harbours potential for error. Coating thicknesses that are too low or too high are not ideal. Electrostatic phenomena can also result in a negative coating pattern, especially with complex geometries. Paint powder does not deposit evenly on the edges and corners of a substrate due to inadequate earthing or excessive current during application, does not adhere partially to the substrate or small craters are created.
Clean work must also be carried out during the firing process. Temperatures that are too high or too low can also cause paint defects.
Error patterns at a glance
Get detailed information from FreiLacke before carrying out a powder coating job. In our clear summary of the typical error patterns, you will not only find out what the underlying causes can be in detail, but also what the ideal solution for the individual problems with the coating looks like.
Powder spitters
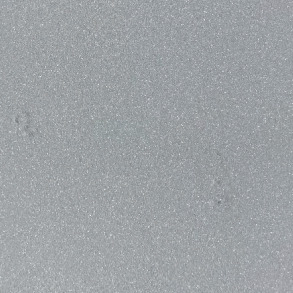
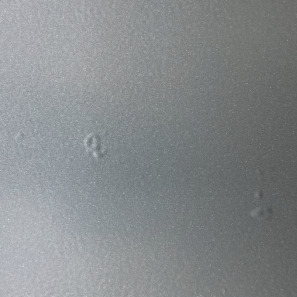
Appearance
- Powder accumulations on the surface
- After the stoving oven, these appear as powder varnish elevations
Causes
- Poor fluidisation
- Wear of the capture nozzle
- Sintering in the injector or powder hose
- Moisture in the powder coating
- Fine-grained powder with poor fluidisability
- If the air speed in the powder hose is too low, this can lead to deposits and powder spitting.
- Circulation operation influences the particle size of the powder coating and therefore the fluidisation.
- Contamination can also favour deposits of subsequent powder and lead to irregular powder ejections.
- Narrowing of the hose diameter.
Solutions
- Check fluidisation
- Check catch nozzle, replace if necessary
- Avoid condensation
- Check earthing
- Measure powder output quantity
- Checking the application parameters
- Use fresh powder
- Check hose routing
- Observe the air parameters - increase the dosing/additional air if necessary. Use hoses with a smaller diameter or radii of at least 150-200 mm.
- Upgrade the powder recovery system with a fresh powder dosing system with level control.
- This ensures that the ratio of recycled powder to fresh powder is correct.
- Check injectors and catch nozzles during daily cleaning, e.g. using a gauge, and replace if necessary.
- Avoid kinks or crushing, e.g. due to cable ties.
Craters / wetting disorders
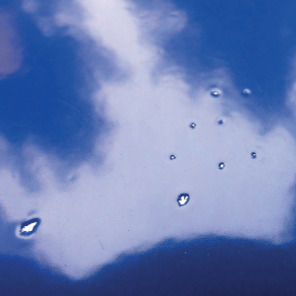
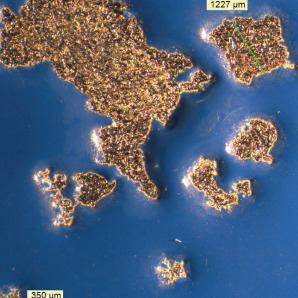
Appearance
- Mostly circular indentations
down to the substrate
Causes
- Silicones, greases, oils
- Inadequate pre-treatment (VBH)
- Contaminated ambient air
- Contaminated powder
- Moisture and / or oil in the compressed air line
- An inadequate VBH does not clean the substrate surface thoroughly. As a result, non-wettable particles such as oils, greases or silicones remain on the component.
- Contamination from incompatible powder coatings.
- If there is oil or water in the compressed air, this can lead to wetting problems.
Solutions
- Ensure cleanliness
- Check the bath parameters (VHB)
- Checking the compressed air
- Check powder coating for contamination
- Re-coat component
- Constant and regular checks of the bath parameters during pre-treatment and the corresponding documentation increase the cleaning effect and service life in the long term.
- Thorough cleaning before changing the powder prevents the mixing of different powder coatings.
- Check and maintain the oil and water separators of the compressed air (e.g. using a mirror test). Create maintenance plans for regular inspections.
Pinpricks
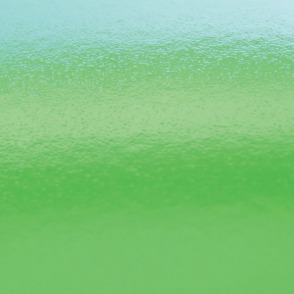
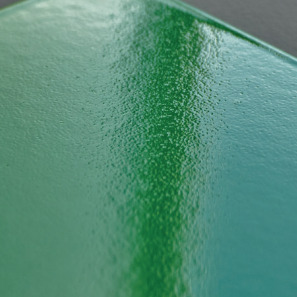
Appearance
- Microcrater / pores in the
coating
Causes
- Layer thickness unsuitable
- Outgassing from the workpiece
- Incompatibility due to other powder coatings
- If the coating thickness is too high, outgassing from the substrate or decomposition products, for example, cannot escape through the coating layer during chemical crosslinking.
- If the coating thickness is too low, a rough, e.g. blasted, surface may not be adequately covered.
- Mixing two powder coating systems can also result in pinholes.
Solutions
- Optimise coating thickness
- Temper the workpiece
- Ensure cleanliness
- The coating thickness should always be checked during the ongoing process and adhered to in accordance with the manufacturer's specifications. This not only prevents errors, but also saves costs.
- Avoid unnecessarily rough surfaces, e.g. during the blasting process.
- Ensure cleanliness before every powder coating change to avoid carry-over/contamination.
Stippling (dirt inclusions)
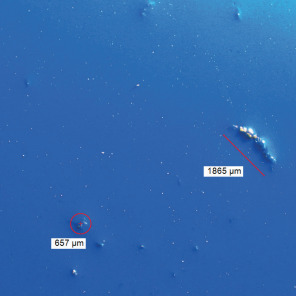
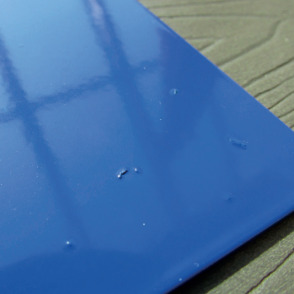
Appearance
- Inclusion of a foreign body in the lacquer surface
- Atypical elevation in the lacquer surface
Causes
- Contamination of system, cabin, conveyor, oven
- Colour change
- Worker: hair, clothing fibres etc.
- Production-related sources of defects such as chips or agglomerates
- If the cabin, conveyor or powder furnace are not regularly maintained and cleaned, dirt can accumulate and be deposited on the components.
- Systems without a screening machine are more susceptible to a contaminated circuit.
- Production-related press fleas or press chips protruding from the paint surface.
Solutions
- Create a cleaning plan.
- Screening machines reduce contamination in the powder circuit.
- Regular inspection of the raw parts leads to a reduction in the defect rate in the painting systems.
- Create a cleaning plan.
- Screening machines reduce contamination in the powder circuit.
- Regular inspection of the raw parts leads to a reduction in the defect rate in the painting systems.
Overburning of the paint layer Embrittlement / yellowing
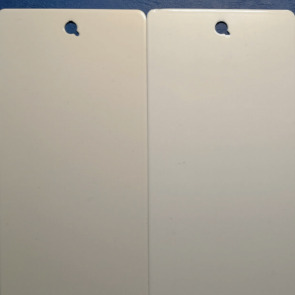
Appearance
- Varies depending on the powder type
e.g. yellow tint with light
powder coating colours
Causes
- Burn-in conditions according to
manufacturer’s specifications not met
- This is usually due to too long a dwell time in the curing oven or too high curing temperatures.
- A directly gas-heated oven can also cause yellowing
Solutions
- Check the furnace parameters
- Check and comply with curing conditions according to the manufacturer
- Observe dwell times and, for example, avoid belt stoppages in the curing oven
- Compliance with the powder coating manufacturer's curing conditions.
- Belt stoppages in the curing oven must be avoided. The oven temperature must be lowered for longer downtimes.
- Use of a gas oven-stabilised powder coating.
Underburning of the paint layer
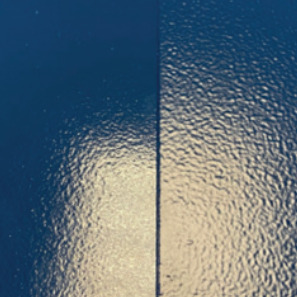
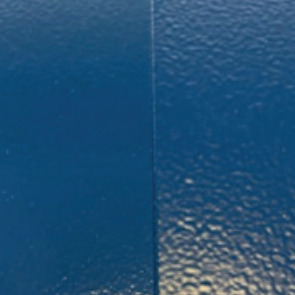
Appearance
- Surface too shiny
- Poor adhesion (scratch test)
Causes
- Burn-in conditions insufficient
- Inadequate curing conditions mean that the powder coating does not fully crosslink. As a result, the chemical and mechanical properties cannot be achieved.
- In the case of matt powder coatings, this can lead to an increase in gloss.
Solutions
- Check curing temperature
- Post-curing the components
- Carry out oven measurement
The curing conditions can be optimised by means of oven measurements.
The rule of thumb is
Curing time of the powder coating system (10min. / 180°C) at 180°C circulating air temperature.
+ 6 minutes for the first mm of object thickness
+ 3 minutes for each additional mm of object thickness
Mangelhafte Erdung
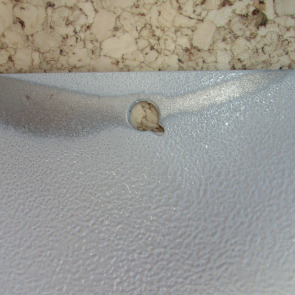
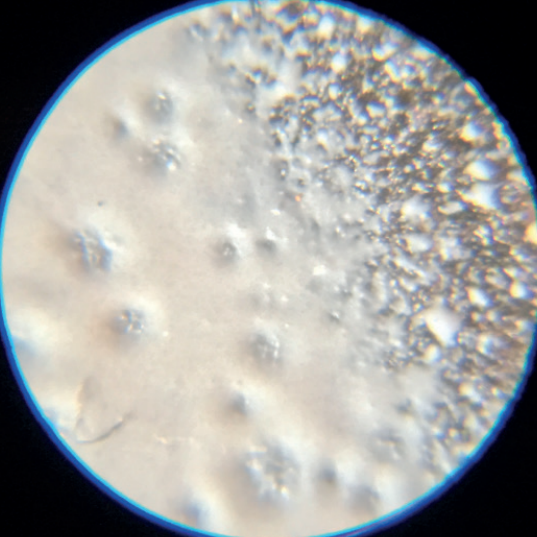
Appearance
- Powder coating does not partially adhere to the object
- Circular stress punctures
Causes
- Electrons cannot flow off completely
- Overvoltage on the component
- If there is no electron discharge, the powder coating cannot adhere to the component.
- This is often shown by circular voltage breakdowns (spray-back effects).
- Coated suspensions have an insulating effect.
Solutions
- Check earthing
- Attach earthing cable
- Use uncoated hooks
- Check component and application for earthing.
- Check earthing cable and attach if necessary.
- Use uncoated suspensions.
- High voltage (kV) and current (µA) should be reduced.
Layer thickness too low
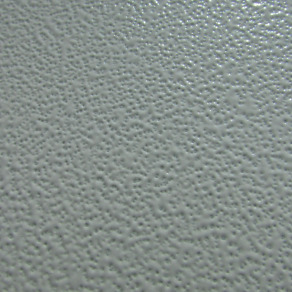
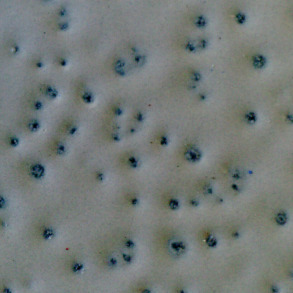
Appearance
- Shining through of the substrate
- No closed powder coating layer
- Surface appears uneven
Causes
- Powder output too low
- Coating time too short
- Powder coating charging not optimal
- Formation of Faraday cage
- Inadequate earthing
- Insufficient powder quantity (conveying air).
- Belt speed too high.
- Worn catch nozzle in the injector.
- Delivery hose sections too long.
Solutions
- Optimise application parameters
- Check coating duration and increase if necessary
- Ensure earthing
- Increase powder quantity or reduce belt speed.
- Charge the powder coating well by optimising the high voltage (kV) and current (µA).
- Check the injector or catch nozzle and replace if necessary.
- Realise short delivery hose sections to achieve optimum powder flow
Layer thickness too high
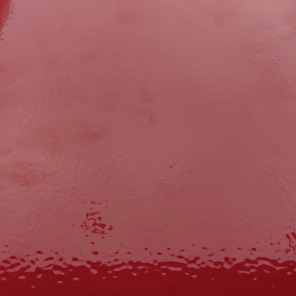
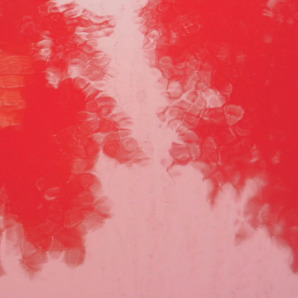
Appearance
Before baking:
- Uneven
After baking:
- Orange peel, pinholes
- Fat edges
- Runner inclination
Causes
- Excessive powder supply
- Excessively high object temperatures during coating
- Unfavourable geometry
- Current too high
- Relation between Vband speed and Vstroke speed not optimal
- An unfavourable component geometry promotes excessive layer thickness build-up.
- Check the sine curve of the automatic application. If the ratio of Vbelt speed to Vstroke speed is not correct, the component remains in front of the powder guns for too long.
- Components too hot before coating.
- Too high an amperage also favours a high coating thickness.
Solutions
- Optimise gun parameters, e.g. reduce powder quantity, voltage, amperage
- Increase distance between powder gun and component
- Reduce coating time
- Do not coat components “hot
- Allow pre-tempered components to cool down for longer; if necessary, check the temperature with a laser thermometer before coating.
- If the component geometry is complicated, changing the suspension often helps.
- Check and, if necessary, optimise the sinusoidal curve of the side-lifting machines so that the dwell time of the components and thus the powder application is reduced.
Picture frame effect
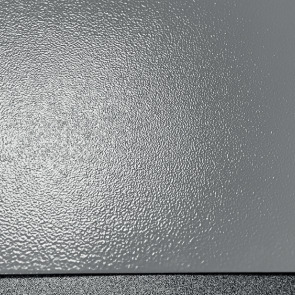
Appearance
- Surface appears uneven
- Increased bulging at corners and edges
Causes
- Amperage & high voltage too high
- Distance between powder gun and component too large
- Powder output too high
- If the high voltage and current are too high, too many electrons are transported to the component. The electric field is strongest at the edges, which is why a thicker layer of powder coating is deposited here. This effect is further intensified if the guns are too far away from the component. This creates a more pronounced wrap. After firing, this appears as a "picture frame" effect.
Solutions
- Reduce high voltage and amperage
- Reduce the distance between powder gun and component
- Use suitable gun attachments (slotted nozzle, impact cone)
- Reduce the amperage, high voltage and distance from the gun to the component. This results in a more homogeneous layer.
- The perimeter can also be reduced by increasing the air speed
Voltage setbacks
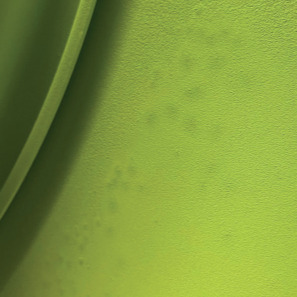
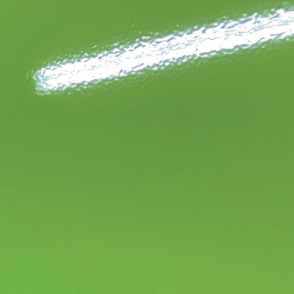
Appearance
- Appear as craters with flow disturbances on the powder coating surface
- Powder coating particles are repelled from the surface (“ice flower effect”)
Causes
- High voltage (kV), current (µA) too high
- Primer or “first coat” has an insulating effect
- Distance between powder gun and component too small
- Insufficient earthing
- Voltage flashbacks are small "explosions" on the powder coating surface. Excess accumulations of electrons, due to excessive high voltage (kV), current (µA), discharge abruptly.
- A primer or second coating leads to a build-up of paint with an insulating effect.
- If the distance between the spray gun and the component is too small, this favours the formation of a stronger electric field.
- Insufficient earthing does not allow the electrons to flow away, which can lead to voltage flashbacks on the surface.
Solutions
- Reduce high voltage (kV), current (µA) and increase gun distance to the component
- Optimise earthing
- High voltage (kV) and current (µA) should be reduced.
- The distance to the component should be increased.
- Check earthing and optimise if necessary.
- The use of an ion trap (e.g. corona ring) can also help here.
Faraday cage Poor penetration behaviour in complex geometries
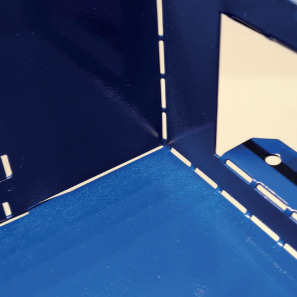
Appearance
- Corners, edges and undercuts are only insufficiently coated
- Extreme differences in coating thickness
Causes
- Conveying / dosing air too high
- Powder output too low
- No optimum nozzle
- Current too high
- Insufficient earthing
- Distance between powder gun and component too high
- If the conveying / dosing air is too high or the distance between the gun and the component is too small, the powder can be blown off.
- If the current / high voltage is too high in 3-dimensional components, the powder coating is difficult to deposit within these geometries.
Solutions
- Reduce conveying / dosing air, current / high voltage or gun distance
- Use tribo application
- Optimise earthing
- E.g. attach corona ring
- Reduce gun distance to the geometry.
- Reduce the conveying / dosing air (soft cloud).
- Reduce the current / high voltage so that fewer electrons are applied. This reduces the Faraday cage and the powder can penetrate corners and undercuts better.
- Reduction of excess electrons by means of an ion trap (e.g. corona ring).
Contamination by foreign powder
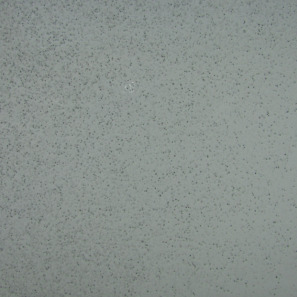
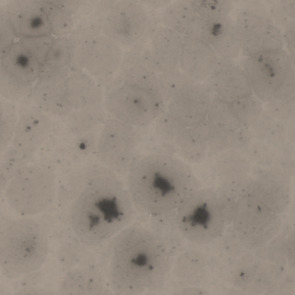
Appearance
- Particles of a different colour on the
lacquer surface
Causes
- Dirty curing oven
- Lack of cleanliness during colour change
- Contaminated conveyor / skid / carriage
- Contamination due to cleaning
- Unfavourable air movements
- System defects (e.g. filter
- Unfavourable air ducts and excessive air speeds in the oven entry area can cause powder particles to be blown off and deposited on other components.
- Powder coating particles can, for example, be deposited on the conveyor chain and fall onto the surface to be coated.
- During cleaning, powder coating particles are often whirled up and can be deposited anywhere.
- If there are system defects, e.g. on the filter or cyclone, this can lead to carryover / contamination in the circulation system.
Solutions
- Check powder enamelling oven and clean if necessary
- Maximum cleanliness during colour change > Contamination!
- Regular cleaning of the conveyor and trolleys
- Optimisation of system cleaning, e.g. vacuuming
- Check the extraction performance of the powder booth
- Regularly check the air flow and air speed in the oven (maintenance schedules).
- Regular cleaning of the system peripherals.
- Ideally, hoovers should be used instead of compressed air guns when cleaning the booths. This can reduce contamination from powder particles in the system periphery.
Contamination from lubricants
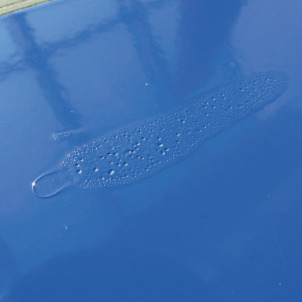
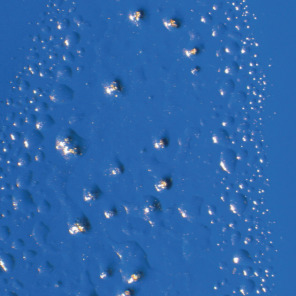
Appearance
- Crater-like flow disturbances in
the paint surface
Causes
- Components contaminated
- Unsuitable pre-treatment
- Oil in the compressed air line
- Contaminated components can cause wetting / levelling faults.
- Unsuitable or defective chain lubrication of the conveyor.
- Oil or condensation in the compressed air line.
Solutions
- Use suitable pre-treatment chemicals
- Check water & oil separator in compressed air line, install if necessary
- Determine suitable pre-treatment chemistry with VBH supplier.
- Regular process control of the pre-treatment.
- Use suitable lubricants for the conveyor. Check through maintenance schedules.
- Check oil/condensation separator, replace if necessary.
Outgassing
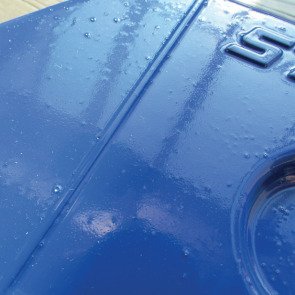
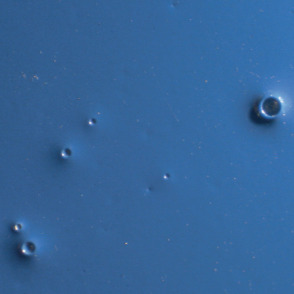
Appearance
- After firing,
pinholes, bubbles or craters
can be seen on the surface
Causes
- Liquid or gaseous inclusions emerge when heated
- Layer thickness too high
- Unsuitable VBH
- Heating can cause gases to escape from hollow chambers / cavities.
- In the case of scooping geometries, moisture residues can cause surface defects.
- Unsuitable pre-treatment can lead to deposits of salt crystals, chemical residues or oils/greases on the surface.
Solutions
- Temper and cool components before coating
- Optimise coating thickness
- Use degassing powder coating
- Tempering the components can reduce / prevent outgassing before the actual stoving process.
- In the case of water-absorbing components, changing the suspension can help.
- Acclimatising the components can prevent condensation forming on the surface.
- Use suitable pre-treatment media.
- Use degassing powder coating.
Poor fluidisation
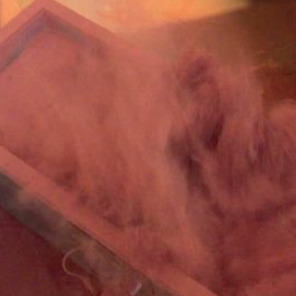
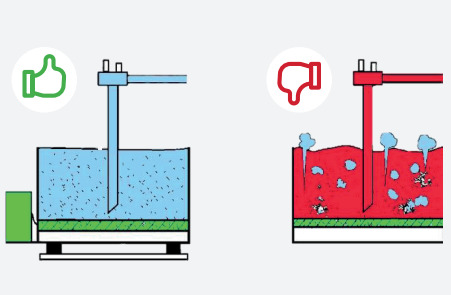
Appearance
- Fountain formation in the fluid container
- Formation of air channels in the fluid container
Causes
- Fluid air too high
- Fluid air too low
- Improper storage of the powder coating
- Defective fluidised bed
- Incorrect fill level
- Too low a fill level in the storage container can lead to inhomogeneous fluidisation.
- In circulation mode, the grain spectrum of the powder coating can become finer, which can lead to fluidisation problems.
- A clogged or defective fluid base has a negative effect on fluidisation.
- Oil or condensation in the compressed air line as well as improper transport / storage conditions can lead to clumping.
Solutions
- Check the fill level of the storage container
- Continuously add fresh powder
- Optimise fluid air
- Clean or replace fluid floor
- Check compressed air for moisture / oil
- Ensure the correct fill level in the reservoir.
- Check the level probe.
- Continuous fresh powder dosing in recirculation mode.
- Clean fluidised bed regularly, replace if necessary.
- Use oil and condensation separators (check by mirror test).
- Observe the transport / storage conditions according to the technical data sheet.
Avoiding error patterns with the experts from FreiLacke
When repairing defects in powder coatings, a precise assessment of the damage pattern is essential. Some defects can be so severe that a complete repair is not possible without compromising the quality of the coating. Removing the existing coating and completely recoating is the best option in such cases.
This makes it all the more important to create ideal conditions before the coating process so that paint defects do not occur in the first place. Among other things, the choice of the correct paint is crucial. Careful preparation and implementation of the coating process is also essential. This includes thorough cleaning of the surface, control of the ambient conditions such as temperature and humidity, correct application of the coating material and regular maintenance and calibration of the coating system used.
Discover our
paint solutions
Cost-efficient, environmentally friendly and highly durable.
Unsere Fokusthemen als Lackhersteller
Anwendungen
Industrielle Pulverbeschichtung
Korrosionsschutz
Anti-Graffiti-Schutz