Interesting facts about
Powder coating
Powder coating is a popular surface finishing process in many industries. It is a technique in which a dry powder material is applied to a substrate and then melted onto it at high temperatures. This creates a smooth and even coating.
This is who we are: FreiLacke is a leading provider of system solutions in the field of coating technology and offers a wide range of powder coatings. The company develops customised products that meet the specific requirements of its customers, fulfil the highest quality standards and follow the system coating concept.
Advantages of powder coatings
High resistance
One plus point is the high chemical and mechanical resistance of this coating solution, which makes it suitable for use in various areas of application. Powder coatings are resistant to wear, chemicals and weathering. They offer a robust and durable surface that is ideal for applications in the automotive, construction, electrical and household appliance industries.
Sustainability
Another advantage lies in sustainability: powder coatings contribute to an environmentally friendly production process, as they do not release any volatile organic compounds (VOCs) and therefore do not affect air quality.
Efficiency in production
By using FreiLacke powder coatings, considerable optimisations and savings can be achieved in the production process. The reduced curing temperature leads to savings in energy consumption and shorter oven throughput times, which in turn increases production speed.
Coating efficiency
The efficiency of the powder coating process is increased by the possibility of recovering and reusing the overspray, which reduces both costs and material waste.
Flexibility
Another advantage is the variety of possible applications and the flexibility in design. Powder coatings are available in a wide range of colours and textures, giving designers and engineers plenty of creative freedom. They can be used for decorative to functional coatings and are suitable for a wide range of substrates.
Suitable materials for powder coatings
Metals such as steel, stainless steel, aluminium and zinc are ideal substrates for powder coatings – due to their excellent adhesion properties. Coatings in powder form provide metals with excellent protection against corrosion and mechanical damage, which extends their service life and reduces maintenance costs.
In the past, powder coatings were only suitable for metallic surfaces. Thanks to FreiLacke, non-metallic materials can now also be finished and sealed.
Glass can also be powder coated to achieve decorative effects and additional strength. This is particularly useful in architectural applications where both aesthetics and durability are important.
Plastics are also often powder coated to make their surfaces more resistant and attractive.
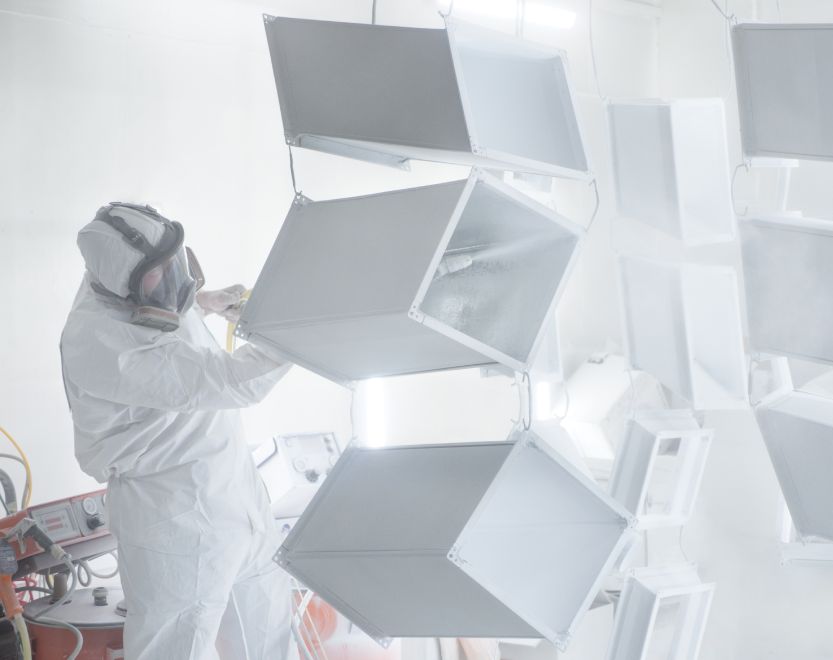
Wide range of applications
Powder coatings have a wide range of applications. In the automotive industry, they are used to coat metal parts to prevent corrosion and extend the service life of components. In the construction industry, they offer a durable and weatherproof solution for facades and other metal structures. Household appliances and furniture benefit from the decorative and protective properties of powder coating, which offers both aesthetic and functional advantages.
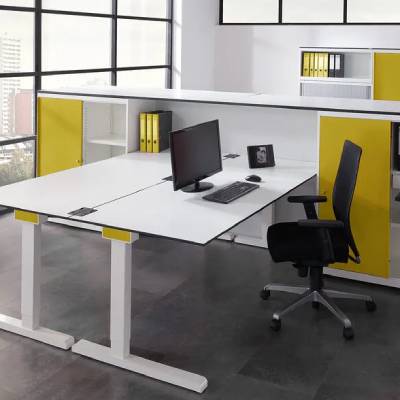
In the furniture industry, metal furniture such as chairs, tables and shelves are powder-coated. This coating not only gives the furniture an attractive appearance, but also a hard-wearing surface that can be used both indoors and outdoors.
The automotive industry uses powder coatings for a variety of car parts, including wheel rims, roof rails, frames and exhaust pipes. These coatings provide protection against weathering and mechanical stress, which increases the longevity of car parts.
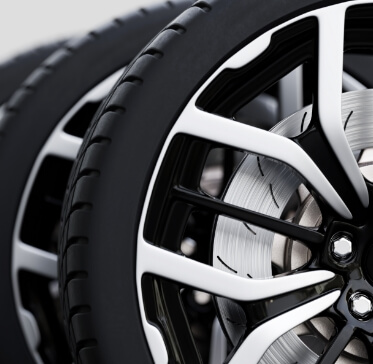
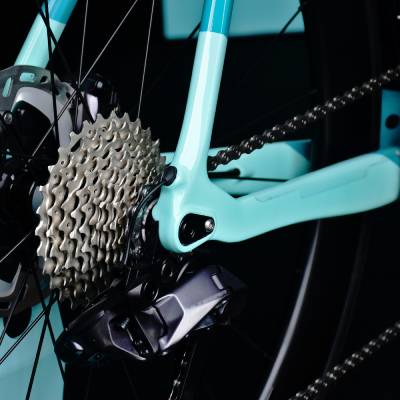
In the bicycle industry, powder coating is often applied to bicycle frames to create a resistant and durable surface that protects against corrosion and scratches.
Powder coatings are also used in the household appliance sector. Manufacturers of fridges, dishwashers and washing machines use this technology to create hard-wearing, easy-to-clean and corrosion-resistant surfaces that meet the high demands of everyday use.
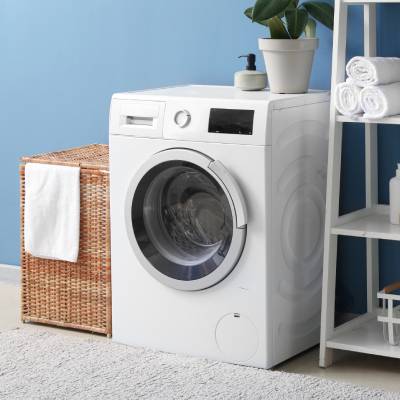
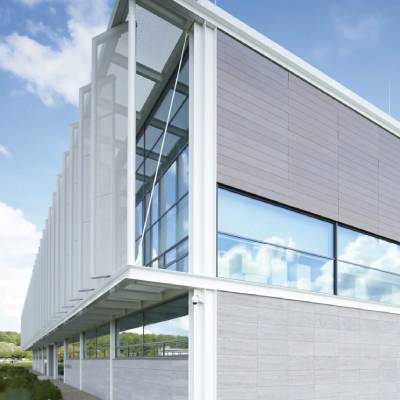
In the construction industry, powder coatings are used for architectural elements such as railings, gates, façade cladding and window frames. These coatings not only offer aesthetic benefits, but also long-term protection against environmental influences, which significantly extends the service life of the components.
Apply powder coatings correctly
Powder coating on a production line
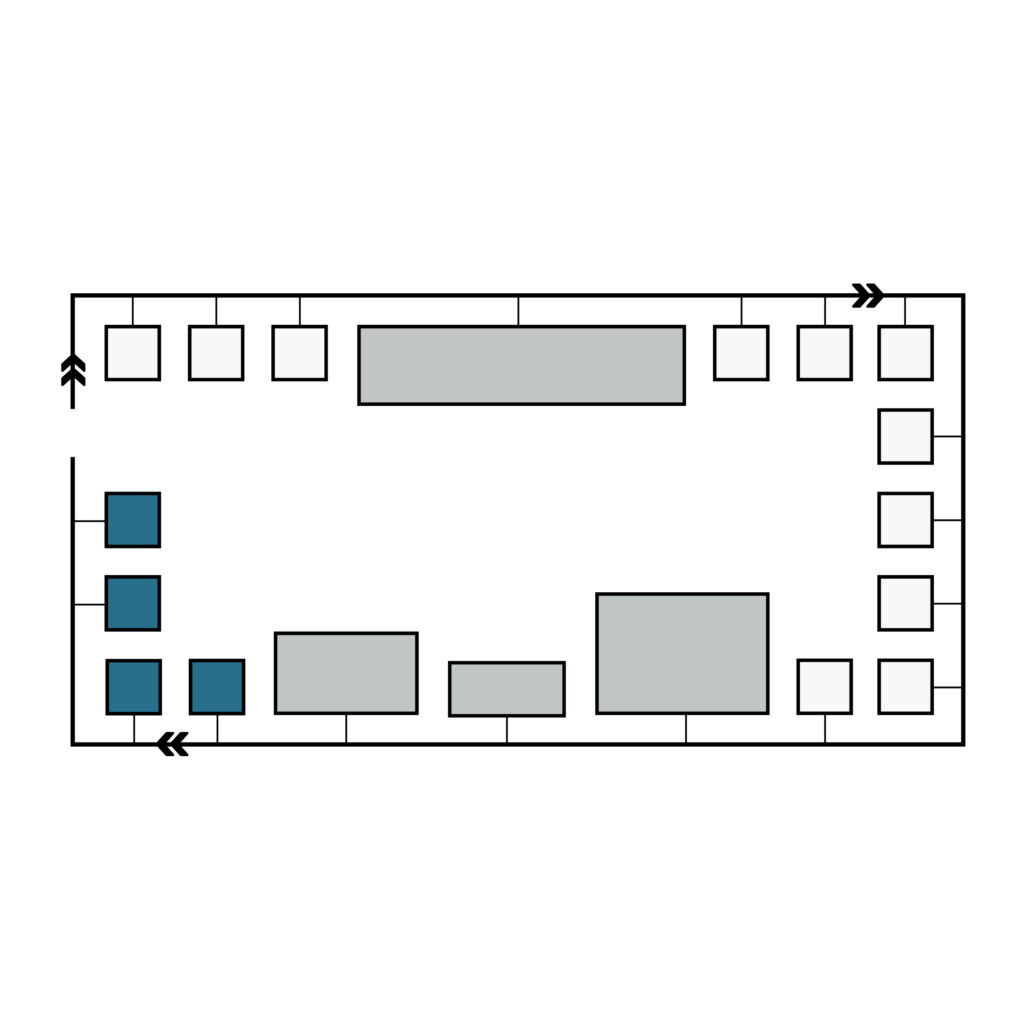
The parts to be coated are installed on the conveyor belt.
1 von 5 2Next, the objects are thoroughly chemically or mechanically cleaned and pre-treated to remove dirt, oil and other impurities.
2 von 5 3The powder is then automatically sprayed onto the electrically earthed object using an electrostatic spray gun. The powder adheres evenly to the surface thanks to electrostatic charging.
3 von 5 4The coated objects are then heated in the oven at temperatures between 150 and 200 degrees Celsius. The powder melts and forms a smooth, durable and robust coating.
4 von 5 5The objects are now protected by a durable powder coating and ready for transport or further processing.
5 von 5Essential pre-treatment
The preparation for a high-quality powder coating involves various steps to ensure optimum adhesion and aesthetics.
The surfaces are cleaned to remove dust, scale, corrosion, oil and other contaminants using mechanical and chemical processes.
Compliance with the dwell time in the oven ensures complete curing of the powder coating.
The earthing of the workpieces is crucial for an even electrostatic charge during the coating process.
In addition, cleaning the application equipment after each process is crucial to ensure consistent quality.
Setting optimum application parameters such as spray pressure and distance is important for an even coating.
The correct curing temperature is also crucial for successful cross-linking of the powder with the surface.
Tempering the workpieces before coating reduces stresses in the material and removes residual moisture, resulting in an even coating without blistering.
Correct layer thickness
The layer thickness is a decisive factor in powder coating, which has a significant influence on the quality and durability of the coating. Ideally, the thickness should be between 60 and 80 micrometres. A coating that is applied too thinly provides insufficient protection and adhesion, while a coating that is too thick can lead to stresses, blistering and cracking. A correct layer thickness increases the durability of the coating and offers optimum protection against corrosion, UV radiation and mechanical influences.
Typical error patterns
When powder coating, various defects can occur if the various parameters and processes are not adhered to, which can impair the quality and aesthetics of the coating. Typical examples include

Blistering due to moisture on the surface to be coated.

Formation of runs, thicker areas of the coating, which mainly occur at edges or corners.
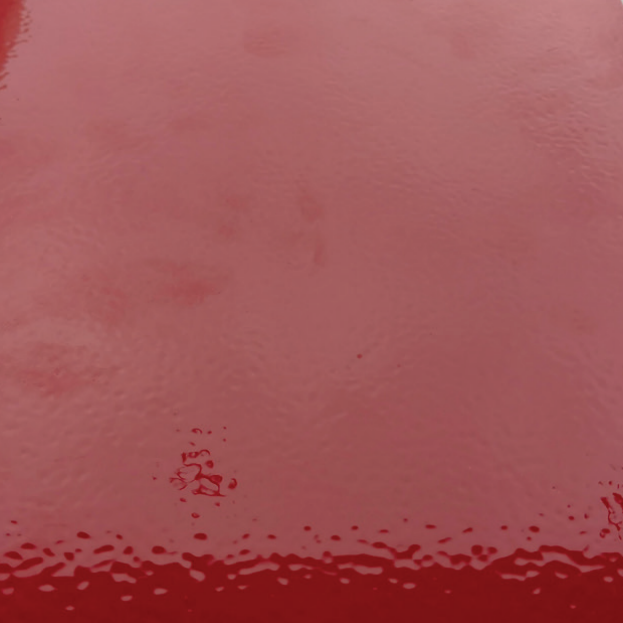
The formation of an orange peel, an uneven surface reminiscent of the texture of an orange peel.
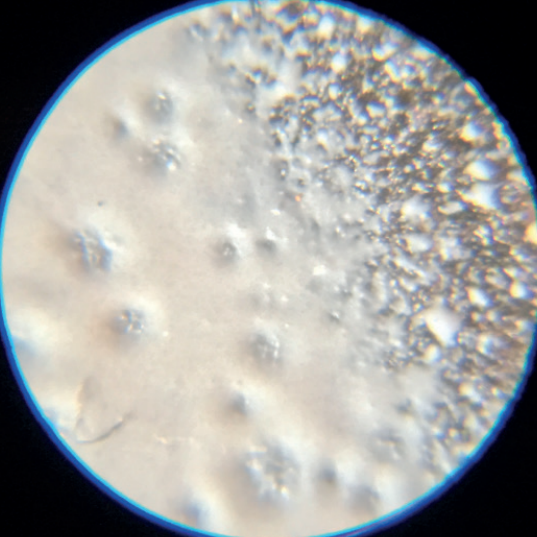
Adhesion problems due to improper pre-treatment or insufficient layer thickness, resulting in peeling, cracking or blistering.
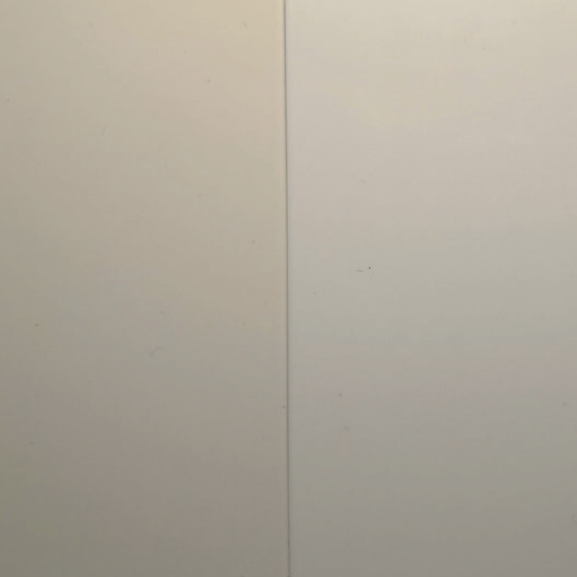
Colour deviations due to an incorrectly mixed powder coating, fluctuating powder coating quality or a coating temperature that is set too high.
Customised powder coating with FreiLacke
A special feature of FreiLacke’s powder coatings is their adaptability to the individual needs of customers. The company offers comprehensive consulting services to find the optimum solution for each specific application. This also includes support with process optimisation and the selection of a suitable coating system.
Energy-efficient powder coatings
Low stoving temperature
Our energy-efficient powder coatings are designed for improved energy efficiency, for example through lower curing temperatures, which reduces energy consumption in production.
System coatings
Horizontal and vertical
FreiLacke powder coatings can be easily integrated into horizontal and vertical coating systems to create durable and visually homogeneous coatings.
Facade
Design & Architecture
Our FREIOTHERM façade powder coatings are designed to provide a durable and attractive coating for building façades. They are specially formulated to withstand weathering and environmental influences while ensuring an appealing aesthetic.
Let us advise you
Would you like detailed advice on our powder coatings in general? Would you like to know more about whether the cost- and resource-saving powder coatings from FreiLacke are a worthwhile alternative for your projects?
We will be happy to provide you with comprehensive advice on all our coating solutions: These include system coatings, industrial coatings for particularly demanding areas of application, as well as electrocoatings. Perhaps you are also interested in other innovative powder coating processes, such as the reproduction of anodised colours with powder coating? Our consultants will be happy to answer your questions in detail. Our experts will describe the method to you in detail and explain its many advantages.
Discover our powder coating solutions
Cost-efficient, environmentally friendly and highly durable.
Unsere Fokusthemen als Lackhersteller
Anwendungen
Industrielle Pulverbeschichtung
Korrosionsschutz
Anti-Graffiti-Schutz