Interesting facts about
Cathodic dip coating
Cathodic dip coating (CDC) is one of the most modern processes in the field of industrial surface coating. Especially in sectors such as mechanical engineering, vehicle construction and the construction industry, companies rely on it to protect components effectively and sustainably. KTL also scores with a more positive environmental balance compared to other painting methods.
What is cathodic dip coating?
Cathodic dip coating, also known as cataphoretic dip coating, is an electrochemical process for surface coating. Workpieces are immersed in a paint solution while an electric current flows. The cathodic dip coating is created on the negatively charged workpiece surfaces.
Here, a chemical reaction causes the positively charged paint particles to form a paint film. Anodic dip coating (ADC) works the other way round. Both coatings belong to the e-coating topic cluster.
Properties of the KTL coating
Excellent corrosion protection
Ideal for demanding environments.
High process economy
Little material loss, optimum surface coverage.
Environmentally friendly
Water-based paint, low emissions.
Uniform layer thicknesses
Also suitable for complex geometries.
Hohe Haftung:
Excellent basis for further coatings
In addition, cathodic dip coating offers reliable protection against damage caused by chemical and mechanical stress. The ability to coat different materials such as steel, aluminium and galvanised surfaces makes it suitable for many industrial sectors.
The process of cathodic dip coating
The cathodic dip coating process goes through several steps to ensure optimum quality and efficiency. Every detail of the process has been optimised to meet the highest standards in coating technology.
Pre-treatment
Pre-treatment of the workpiece ensures adhesion and the quality of the coating. As a result, the paint not only adheres better to the surface, but also protects against corrosion.
- Degreasing: Oils, grease and other impurities are removed in special cleaning baths. This prevents foreign substances from impairing paint adhesion.
- Pickling: This chemical treatment removes rust and oxide layers. This step is particularly essential for metal parts that have been stored for a long time in order to expose a clean metal surface.
- Phosphating: A thin layer of phosphate is applied to the surface. This serves as an adhesion promoter between the metal and the paint layer. It also provides additional corrosion protection.
Immersion bath in the cathodic dip coating
The actual coating process takes place in the dip tank. The workpiece is completely immersed in a paint solution consisting of a water-based dispersion.
- Application of the current: Cathode polarisation of the workpieces attracts the paint particles from the solution and forms the paint film on the workpiece surface through a chemical reaction. This leads to an even coating formation on the entire surface.
- Uniform coating: A decisive advantage of CDC is that even complex geometries, narrow cavities and hard-to-reach areas can be reliably coated. This distinguishes CDC significantly from other processes, which reach their limits with such components.
- Coating control: The thickness of the coating layer is precisely controlled by the current voltage and the coating time. This allows customised results to be achieved for different requirements.
The paint solutions from FreiLacke are formulated to offer both excellent corrosion protection properties and a high level of environmental compatibility. Through regular quality controls, FreiLacke ensures that the paint solution constantly maintains its optimum composition.
Rinsing and drying
After the dipping process, the workpiece is further processed in several steps.
- Rinsing: Excess paint is removed by rinsing baths. This process is important to achieve an even and smooth surface.
- Drying and curing: The coating is cured at high temperatures in a special oven. This gives the coating its final hardness, durability and adhesion.
At FreiLacke, this step is carried out with minimal energy consumption while maintaining the highest quality standards. Special sensors and control systems monitor the entire drying process to ensure that each workpiece cures evenly.
Advantages of cathodic dip coating at a glance
Almost 100 % material efficiency through recovery of excess paint
Even coating, even in hard-to-reach areas and cavities
Reduced material consumption and automated processes cut costs
Environmentally friendly thanks to water-based solutions and low emissions
Can be used flexibly for different materials and geometries
Advantages of cathodic dip coating compared to other processes
CDC differs from alternative processes such as powder coating or wet painting in many respects. In addition to its environmental friendliness and material efficiency, it is characterised by its versatility. A wide variety of materials and geometries can be processed using the same process, making it a universal solution for many branches of industry.
Thanks to the almost complete recovery of excess paint, material consumption is reduced to a minimum.
Another clear advantage is the depth effect of the process. Even hard-to-reach areas and cavities can be coated evenly. The automated processes also ensure high productivity, as hardly any manual reworking is required.
Compared to wet painting, cathodic dip painting is not only more efficient, but also more environmentally friendly. Water-based solutions minimise emissions and protect the environment. Powder coatings, on the other hand, often reach their limits when it comes to components with complicated geometries.
Application of the cathodic dip coating
The versatility of cathodic dip coating makes it an indispensable process in many industries.
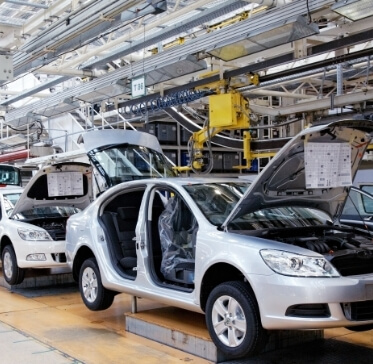
Automotive industry
Body and chassis parts, engine mounts and axles
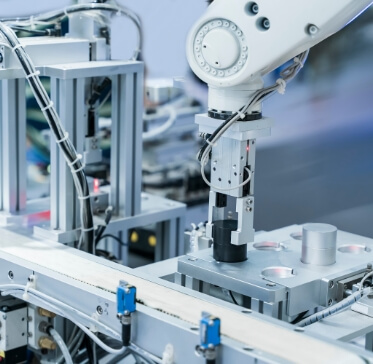
Mechanical engineering
Corrosion protection for large and complex components
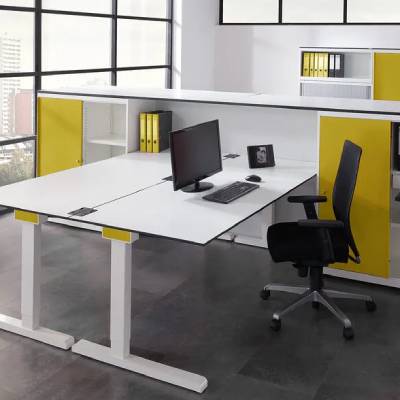
Furniture industry
Metal frames and fittings that require both protection and visual quality
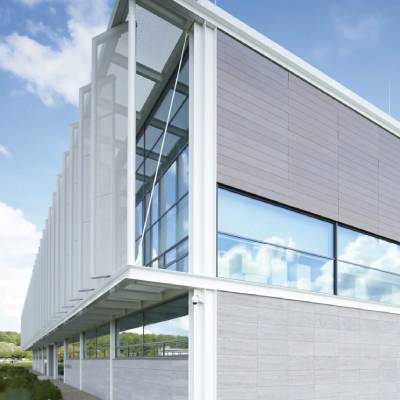
Construction industry
Load-bearing metal structures, railings and other construction elements
The cathodic dip coating is particularly suitable for: Steel and stainless steel, aluminium and alloys and zinc-coated surfaces. The ability to coat combinations of different materials considerably expands the range of applications for CDP.
FreiLacke - Your partner for cathodic dip coating
FreiLacke offers high-quality cathodic dip coatings that are specially tailored to the needs of industry. You benefit from personalised advice, during which our team of experts develops solutions that precisely match your requirements.
Thanks to decades of experience in industrial painting, with FreiLacke you have a competent partner at your side. We also promote sustainability through environmentally friendly products and processes.
In addition to high product quality, our company naturally also offers a comprehensive range of services. Technical training courses ensure that your employees can get the most out of our coating products. FreiLacke supports you with individual process optimisation to make your production processes more efficient. Thanks to reliable logistics, we also guarantee fast and safe delivery so that you can realise your projects on time.
Entdecken Sie unsere Tauchlacklösungen
Cost-efficient, environmentally friendly and highly durable.
Unsere Fokusthemen als Lackhersteller
Anwendungen
Industrielle Pulverbeschichtung
Korrosionsschutz
Anti-Graffiti-Schutz