Interesting facts about
Anodic dip coating
Anodic dip coating (ADC) is a proven process for industrial surface coating. This type of coating is primarily used in the radiator, automotive, mechanical engineering and electrical industries. In this way, components are provided with an even and durable protective coating. The process enables precise coating even on complex geometries. ATL not only ensures optimum corrosion protection, but also impresses with its environmentally friendly approach thanks to the use of water-based coating solutions.
What is anodic dip coating?
Anodic dip coating is an electrochemical process for coating metal surfaces that is frequently used in the automotive and mechanical engineering industries. The workpiece is immersed as an anode in a conductive immersion bath containing a water-based paint solution. The ATL coating is created on the positively charged workpiece surfaces. Here, a chemical reaction causes the negatively charged paint particles to form a paint film.
The dipping process is followed by thermal curing, which makes the coating robust and durable. An ATL is particularly suitable for primer protection and interior applications.
Together with cathodic dip coating, ATL is part of the e-coating cluster.
Advantages of anodic dip coating
Uniform coating
Even with complicated shapes and cavities.
Corrosion-protected
Good resistance to rust and chemical influences.
Environmentally friendly
Water-based paints reduce the use of solvents.
Efficient
Fast process with low material loss due to recovery.
Adhesive
Excellent adhesion for subsequent coats of paint.
Durable
Resistant coating against mechanical loads.
Excellent colour stability
Very good resistance to UV exposure.
These advantages make ADC particularly attractive for durable, robust and economical coatings.
Cathodic versus anodic dip coating
Anodic and cathodic dip coating (CDC) are electrocoating processes for surface coating.
Both differ significantly in terms of the current flow and their specific applications.
In ADC, the workpiece is connected as the anode, whereas in CDP it is the cathode.
Due to its better corrosion resistance and adhesion to many metals, CDP offers an advantage over ADC - particularly in the automotive industry.
ADC, on the other hand, is particularly suitable for primers and applications where high UV stability and colour stability are required and corrosion protection is less critical due to the primarily interior application.
Both processes are environmentally friendly as they use water-based paints.
The process of anodic dip coating
Preparation
Before the ATL coating process, the workpiece is cleaned and chemically pretreated to ensure optimum adhesion of the paint.
Dipping bath
It is then immersed in a water-based paint bath consisting of a dispersion of paint particles. The workpiece acts as an anode in a direct current circuit. This causes the negatively charged paint particles to migrate to the surface, where they form a uniform coating through a chemical reaction.
Hardening
After the dipping process, the paint layer is thermally cured in an oven. This makes it robust and resistant to mechanical stress, chemicals and weathering.
Advantages compared to other methods
In contrast to various other paint processes, anodic dip coating, or electrocoating methods in general, enables precise and even coating. Very good results are achieved even with complex geometries and internal cavities, as the paint particles are electrostatically attracted and evenly distributed on the surface.
E-coats reliably protect metal surfaces from environmental influences and are more environmentally friendly than other conventional processes thanks to their water-based materials. The electric coating processes offer versatile application options for a wide range of industries and also allow an aesthetic colour design with UV-resistant, glossy surfaces.
Application of the ADC coating
Anodic dip coating is used in various industrial contexts, particularly where uniform coatings and corrosion protection are essential.
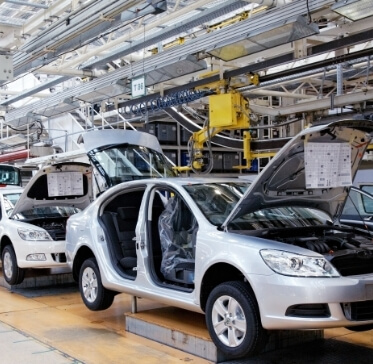
Automotive industry
Priming of car body parts, wheel rims and engine components, especially for simple components.
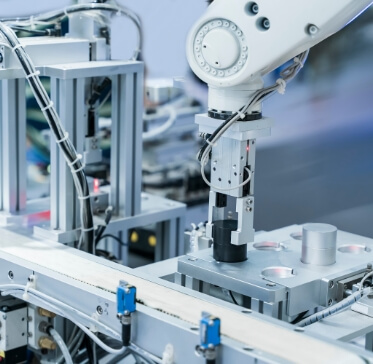
Mechanical engineering
Protection of metal parts such as housings, tools and assemblies against weathering and mechanical stress.
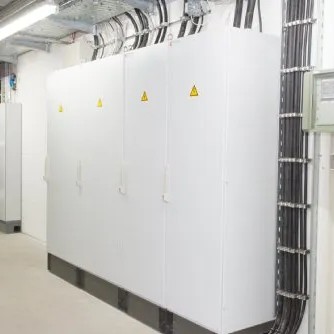
Electrical engineering
Coating of metal parts in electrical devices or control cabinets.
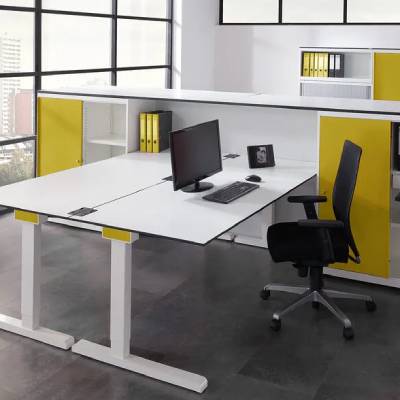
Furniture industry
Protection of metal frames and fittings, which must be durable and rust-resistant.
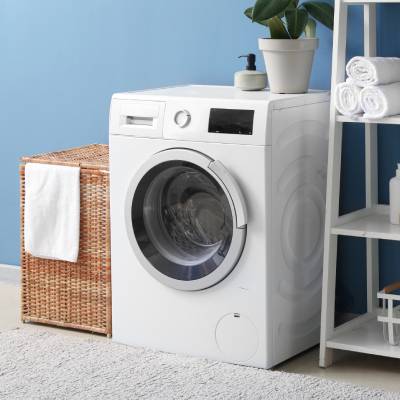
Household appliances
Coating of metal parts in appliances such as washing machines or refrigerators.
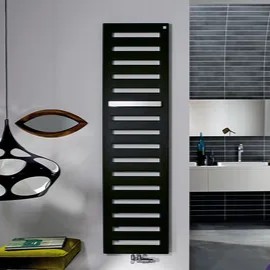
Radiator industry
Primer for steel and aluminium radiators.
The ADC is ideal for applications where cost and environmental efficiency are paramount, but less suitable for highly complex protection requirements. It is particularly suitable for coating the following materials: steel, aluminium, cast iron, stainless steel, zinc, copper, magnesium and alloys (e.g. aluminium alloys).
FreiLacke - Your partner for anodic dip coating
FreiLacke offers high-quality anodised dip coatings that are tailored to the requirements of modern industrial applications. Our team of experts develops customised solutions that are precisely tailored to your needs.
Sustainability is always the focus of our coating solutions: we rely on environmentally friendly, water-based paints and optimised processes to conserve resources while always guaranteeing the highest quality. In addition to dip coatings, FreiLacke offers powder coatings, liquid coatings and vertical and horizontal system solutions.
With decades of experience in surface coating, FreiLacke is your reliable partner for durable and efficient coating systems.
Discover our dip coating solutions
Energy and cost efficient, environmentally friendly and versatile in use.
Unsere Fokusthemen als Lackhersteller
Anwendungen
Industrielle Pulverbeschichtung
Korrosionsschutz
Anti-Graffiti-Schutz